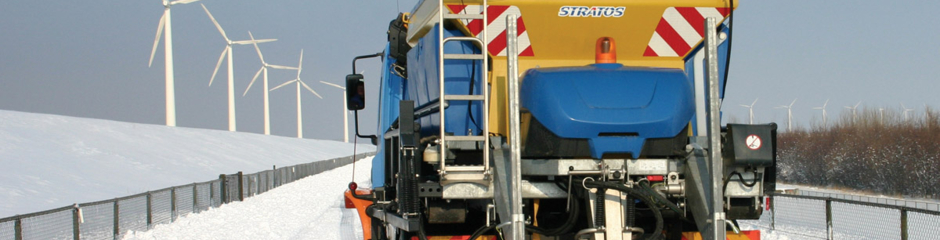
Aebi Schmidt, market leader in road de-icing solutions, has taken a major step in automating the production of its salt spreaders by investing in a Valk Welding welding robot system.
The Dutch location in Holten took this step after deciding to place the production back under its own management. The new system, which consists of four workstations operated by two welding robots, is configured for a capacity of two to three thousand salt sprayers a year. Valk Welding delivered the entire system on a turnkey basis, including the robot programs for the first products, DTPS offline programming software for maximum programming flexibility, training for the programmers and operators, wire feed systems for both robot systems and Valk Welding's own welding wire for a consistent welding process.
In one of Aebi Schmidt's large production halls in Holten the 32 metre welding robot system immediately underlines the high-tech nature of the manufacturer of salt spreaders, Schmidt road sweeping machines and multifunctional vehicles. With their streamlined, modern design, their sustainable construction and innovative technology, the salt spreaders are situated at the high end of the market. Up until recently only the assembly took place at the Dutch location, where the salt sprayers are built for the European market, and the welding was outsourced to suppliers. When the company was taken over by the Swiss Aebi in 2008, the new strategy resulted in a drastic change being made to the production and assembly process. Third-parties were used only for the plating components. From then on the assembly and coating were carried out under the company's own management.
The need for welding automation
The production management in Holten quickly found itself facing a problem owing to the shortage of professional welders. Welding automation was therefore given the highest priority alongside the investment in a powder coating plant. Head of procurement Harald Bloemers: "We approached five parties for this purpose, two of which immediately dropped out because they were unable to meet our requirements. As well as assessing the test welds, the service organisation, the number of installed welding robot systems and the conditions, we focused sharply on what the robot integrators were able to offer in the programming area. It was also important to click with the new supplier. The demo at Valk Welding went more smoothly than with the other candidate and we immediately had more confidence in Valk Welding's offline programming."
Welding robots on two 16 m tracks
Valk Welding built a double system consisting of welding robots suspended on a 16 metre track, each of which operated two 7.5 metre work stations. While a complete chassis was welded on one station, the next chassis was clamped on the station next to it. That made it possible to operate the welding robots virtually continuously. The double design created sufficient capacity to complete the annual production in a 1-shift roster. Some 15 to 20 chassis are produced a day during peak season.
Offline programming
The turnkey delivery included the programming of the largest components, such as the single chassis for the salt spreaders, so that Aebi Schmidt was able to get down to work as soon as the welding robot system was commissioned. Two employees of Aebi Schmidt had already received operator and programming training during the assembly phase at Valk Welding in Alblasserdam. These programmers are now working on the welding programs for the other components the company plans to weld with the welding robots. Harald Bloemers: "The 3D CAD data of the individual components is imported in DTPS, and the components are then placed in the jig, after which the position of the welding torch, the torch angle and the right welding parameters are programmed. The offline programming software has a short learning curve: the programmers were quickly able to use it. Knowledge is also exchanged with other programmers during the annual users club at Valk Welding. DTPS is a perfect tool because everything can be prepared externally outside of production and every detail can be programmed with great precision. Most of the programmes can be used virtually unchanged directly on the welding robot. We will need to programme a total of between six and seven hundred different program ourselves, and we've now completed about 30% of them."
No more need for temps
“The double capacity means that we can complete the welding work with a fixed team of employees without having to take on extra temps. Also, both of the cells have sufficient buffer capacity to absorb any additional growth. Even more importantly, we are now able to achieve a consistent welding quality, which is a big gain compared to manual welding, especially for the larger lengths," explains Harald Bloemers.
Complete system from one supplier
“Valk Welding has a lot of welding and robot know-how, and a great deal of experience with offline programming. That was the combination that swung it for us. It is also important that Valk Welding supplies a complete system. Since we can obtain everything from a single supplier, including the welding wire, we also have just one point of contact that bears the responsibility."
www.aebi-schmidt.nl