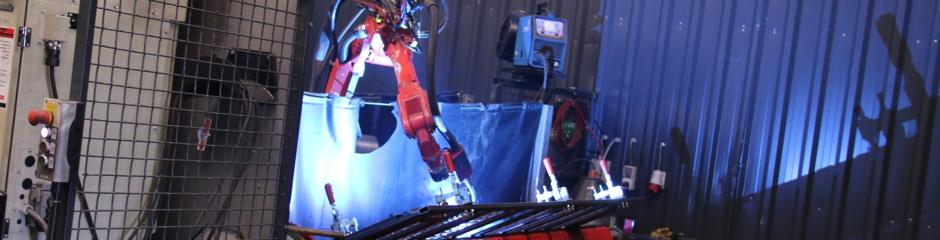
In 2008 Santbergen Rolcontainers decided to start producing its own roller containers as well as repairing them.
That turned out to be a good move for the Breda-based family firm. With annual growth figures of 10 to 15%, thousands of roller containers and other logistics storage equipment are 'rolling' out of the production halls. To keep pace with all the welding this requires, a Valk Welding welding robot with two work stations was taken into use last year. In view of the favourable market developments the brothers Vincent and Edwin Santbergen expect that more will be needed in the years to come.
'Specialists in roller containers' is what Vincent, Edwin and Rebecca Santbergen intended to be when they took over the company from their father Hans. Up until that time Santbergen Rolcontainers had concentrated exclusively on repairing roller containers, both at their own workplace and at customer locations. Edwin Santbergen: "By carrying out repairs we found out which aspects of the roller container were open to improvement. Armed with that know-how we began designing our own roller containers, starting with demos and smaller series. That number soon went up. Since that time the volume has been growing by 15% a year. The company is also continuing to repair, modify and rent out roller containers.
"Making life easier for our customers"
"There are about four roller container manufacturers in the Netherlands, and we try to stand out as a total supplier. We do that not only by delivering top quality Dutch products, but through customisation, short delivery times and providing a highly rated repair service. Customers can also come to us for single roller containers or other logistical storage equipment and to rent various types of roller containers to cover peak periods, for example. By doing this we are penetrating more and more new markets that have never previously used roller containers. To continue to deliver that high level of quality we needed to continue to automate our production process in order to remain competitive on the price aspect as well," explains Vincent Santbergen.
First experience gained with old welding robot
The company took its first steps towards automating the welding production as far back as ten years ago. Edwin Santbergen: "The idea was to start by gaining some experience with this. But we soon found ourselves facing the old technology that was no longer in keeping with the digital methods of today. When we wanted to upgrade the robot we had to pump more and more money into the old system. That told us that the time had come to try something new. Alcomij, a partner of ours, advised us to take up with Valk Welding for their technical know-how, service, training and reliability.
Welding robot on H-frame
The Santbergen brothers first considered the concept of a welding robot with a turntable. Valk Welding came up with another proposal: a welding robot on an H-frame, which makes it possible to produce on two sides and keep more space for the loading and unloading of materials and finished product. Vincent Santbergen: "This is an important aspect, as production has more than doubled. The welding robot system was supplied and completely assembled on the frame, including the Panasonic TA1400 WG welding robot, control panel, drum of welding wire, light curtains and safety screens. Both sides are fitted with a work station with a manipulator so that the welding robot can optimally reach all positions. We made all of the jigs with a simple clamping system ourselves."
Training close to home
"Together with some manual welders we followed a programming and operating course with Valk Welding in Alblasserdam. We weren't all that keen at first: everything was new, including programming on a teach pendant. But the course was very informative and immediately created confidence. This made it possible for us to programme the frames of the roller containers that are now processed by the welding robot in large series. Now that we're getting the hang of it we're gradually extending the process to other parts in smaller series sizes."
Further automation
Edwin Santbergen: "We gradually noticed that we were unable to supply the welding robot with sufficient material quickly enough. The weak link was the existing band saw in which we had to manually place the tubes one by one. That problem has been solved with the new sawing machine with a cassette. The welding robot is now taking up the extra production in addition to what is done by the manual welders. But there's a big quality difference with the robot. That's why we want to have more frames processed by the welding robot. We expect to be able to do all of the welding with robots within 2 years."