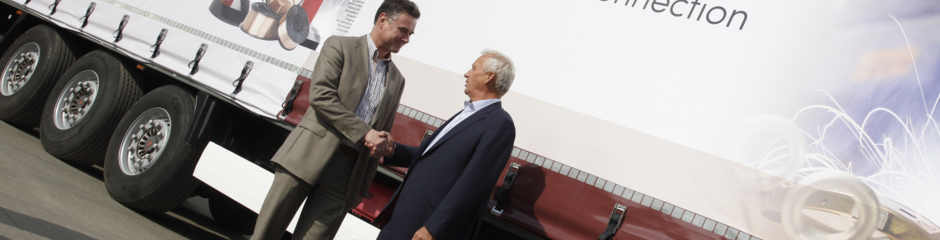
Agrostroj Pelh?imov, Central Europe's biggest subcontractor with an annual turnover of approximately 185 million euros and almost 2000 employees, has begun investing in Valk Welding welding robot systems.
The first of the twelve systems in total has now been delivered. With more than a hundred welding robot systems already in operation, Agrostroj Pelh?imov is taking the step towards higher productivity and flexibility, mainly because of the use of offline programming.
As well as supplying parts for manufacturers of lorries, building machinery and forklift trucks, Agrostroj Pelh?imov builds complete agricultural machines for leading farming machinery manufacturers (see www.agrostroj.cz). These include self-propelled harvesting machines, rotary mowers, soil processing machines (mulchers) and manure spreaders, which are produced from the beginning in components, then coated and assembled at the 175,000 m2 industrial complex. Then they are transported from there to the end-dealer or importer. For this purpose the company has its own transport division with 100 lorries, a number of which have advertising signs promoting the new partnership with Valk Welding.
Strong growth in annual turnover
With turnover increasing from 14 million euros in 1997 to approx. 185 million last year, Agrostroj Pelh?imov is clearly expanding at a rapid pace. Despite this, the manpower level has risen during that period only from 1,200 to 1,965, which is less than would normally be expected given the growth in turnover. This is the result of the extensive automation introduced in the plate processing, coating and welding production operations. The company has 36 laser cutting machines, more than a hundred welding robots, large machining centres and an Eisenmann coating lane with a capacity of 6 x 2.5 m, equipped with the latest production technologies such as a KTL priming submersion pump system and powder coating.
Strong global position
According to owner and CEO Lubomir Stoklásek the company has gained a strong competitive position thanks to the high added value over the entire production chain, from engineering to the ultimate final assembly and direct delivery to the importer. The fact that all of the components are produced in-house enables Agrostroj Pelh?imov to achieve major logistical gains, a high level of flexibility and safety in production. The subcontractor has thus succeeded in building up a strong and long-lasting partnership with its OEMs, which has made it possible for Agrostroj to grow to be Europe's biggest subcontractor. “We have nothing to fear from the competition, even from China and Turkey”, says Stoklásek.
Biggest employer in the region
For each OEM customer there is a project team led by a senior engineer who is responsible for engineering, tooling and production. The entire order administration system for the OEM partners is completely integrated in the ERP system of Agrostroj Pelh?imov. Commercial director Jaroslav Haban: "This full service leaves our OEM partners free to concentrate on their core activities, such as design, marketing and sales."
The company is also the region's biggest employer, and 42% of its employees have received intermediate or higher technical education and the average age is 36. "This is the result of our staffing policy, which is aimed at active partnership with schools for professional education.
Sheetmetal production as core business
Agrostroj has a large number of machines for cutting (36 laser cutting machines), bending and welding and processes over 50,000 tons of steel a year. The sheetmetal production is the most important link in the production chain. In the most recently added production hall of 30,000 m2 is the production has been developed into a line production system based on the 'Lean' principles. This more advanced production automation gives Agrostroj the benefits of a large system supplier, which makes it possible for it to produce faster, more flexibly and more efficiently than its competitors.
Robotisation of welding production
Welding robot systems dominate most of the production lines, which means that the welding production at Agrostroj is at a high level. The company had already spent some time looking for another welding robot supplier with knowledge and experience of offline programming and which could meet Agrostroj's requirements. It emerged from talks with Valk Welding that Valk Welding's systems could yield many benefits in terms of the concept, the programming method, lead times, weld seam monitoring and so on. Valk Welding CZ delivered its first welding robot cell in the production line in 2013. The first products were programmed offline by personnel of Valk Welding CZ so that the cell could be used for production straight away. The results met the quality and productivity requirements and were the decisive factor for the orders for more Valk Welding welding robot systems, 13 systems are now installed
Service and support
While the systems were being built in the Netherlands, Valk Welding provided direct support from its location in Mosnov (Ostrava region). Jakub Vavre?ka, responsible for the activities of Valk Welding CZ: “We provide full support for the people who work with our welding robot systems in the Czech Republic, Slovakia and Poland. That way we can be sure that the welding robot systems are used optimally. The intensive partnership has made it possible to quickly resolve any problems that have arisen up to now."
Towards a doubling in turnover
Agrostroj’s owner Stoklásek: "We are currently processing 50,000 tons of steel a year. Based on our aim of doubling our turnover by 2020, consumption will increase by 20,000 tons a year. We are now working together with a number of customers on making preparations for new products. The complexity aspect means that it can take 2 to 3 years before we are able to make a start with serial production. We will also need modern production technologies, including welding robots, for all those new products.
The benefits of the welding robot systems of Valk Welding and their support made it possible to start production very quickly. The special advanced offline programming system, the 'Quick Touch' wire monitoring system and many other special functions made a strong contribution to this. Combined with the reliability of the welding robot systems that we are increasingly seeing among our customers, we believe that the partnership between Agrostroj and Valk Welding will be mutually beneficial."
www.agrostroj.cz