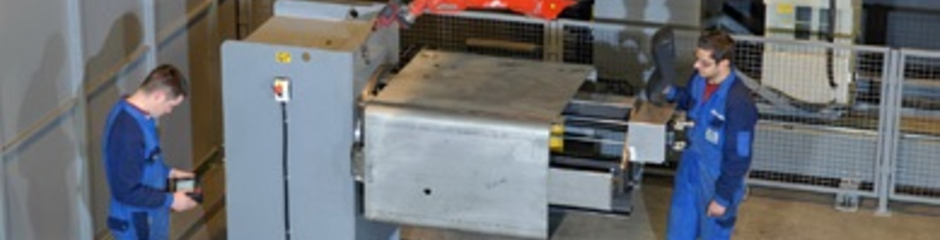
Following an intensive, multiple-year partnership and plenty of testing, machine building company KARL HUGO AG and Valk Welding have succeeded in designing a robotized solu?tion for welding stainless steel pressure vessels.
Following an intensive, multiple-year partnership and plenty of testing, machine building company KARL HUGO AG and Valk Welding have succeeded in designing a robotized solu-tion for welding stainless steel pressure vessels. The applicati-on for these products is viewed as a huge achievement for the industry, considering the level of complexity, the extremely close tolerances, and the high demand set on the density of the welding joints. The small quantities were initially seen as a negative parameter; but, Valk Welding found a solution for that as well. The switch to the robotized welding system me-ans that the machine building company can produce better quality pressure vessels with a much shorter operation cycle.
Welding this type of pressure vessel (auto-claves), used for sterilization purposes in hospitals, etc. is very labour-intensive; the welding seams must be one 100% secure. Director Bernd Hugo explains, “We want to set a new benchmark in quality for the mar-ket with the introduction of these sterilisa-tion systems. However, we kept running into difficulties due to the limits of the manual welding process. You can only fine-tune the welding process well enough to achieve, and maintain, the highest standards of quality by means of robotized welding.”
This solution required a system supplier with a constructive approach to the problem
Brothers, Bernd and Stephan Hugo, first met Valk Welding in 2009, after which both par-ties came together to discuss solutions for welding stainless steel pressure vessels. This meeting resulted in an intensive course of action that led to the success of the project. Bernd Hugo adds, “An automation problem of this level of complexity requires a robot supplier who can deliver a complete system solution, not just a robot. Most welding robot integrators only sell machines, but Valk Weld-ing could offer us a solution that guaranteed success. We realized that Valk Welding was a flexible company with the necessary know-how on arc welding and who appreciated the project as an interesting challenge.”
The switch to robot welding
Welding and machining operations are KARL HUGO AG Maschinenbau's two core compe-tencies; the machine building company has a hall specifically designed for these operations. Due to its high precision machining opera-tions on large pieces weighing as much as twenty tons, KARL HUGO AG is a level above its rivals on the market. The competitive advantage of the company can also be linked to its ability to hermetically seal, by welding, larger pieces on pressure and vacuum vessels for the power industry, the health-care sector, the chemical industry, "raw materials", etc.
Bernd Hugo continues, “Welding large pieces, particularly those made of stainless steel, is very detrimental to the health of the welder, and the work is both strenuous and mo-notonous. Consequently, a welding robot can make the work easier for the manual welder in certain applications. The change from us-ing a welding torch to a teach-pendant is an interesting and informative move for a skilled worker, just like the previous transition from conventional machining operations to CNC operations.”
Getting to know the process
KARL HUGO AG 's welders learned, step-by-step, about robot welding by using a rented welding robot; which allowed them to weld and test the first pressure vessel prototypes internally. The test phase is essential since the welding seams shall be according to the requirements of DIN EN ISO 5817 B. The finished product may only be delivered after our own quality control department has examined them following the guidelines of the 97/23/EC Pressure Equipment Directive, Module H,H1. The company always discussed the results with Valk Welding during the test stage so that we could develop the process from the angle of the supplier as well. The order for the construction and delivery of the welding robot equipment in its definite form was placed in late 2011.
A welding robot on a portal system
The robot welding installation had to be suit-able for welding pressure vessels that varied between 1.3 and 12 metres in length. Accord-ingly, the Panasonic TA 1800 welding robot is suspended from a five meter-high moveable construction that can be driven along an eight-meter track.
To prepare for the delivery in 2012, three welders attended a programming course at Valk Welding's offices in Alblasserdam. Bernd Hugo articulates that “We spent a lot of time during the first six months getting to know the new equipment, the process and the programming, but now we are working at our top manufacturing capacity and we can weld high-grade, double-walled pressure vessels in series. Both the welding process and the fin-ished products are ‘TüV geprüft’. In addition to saving a considerable amount of welding time, we have managed to reduce the target time to minimum."
Ready for more expansion
Currently, KARL HUGO AG delivers one pres-sure vessel per week, but expects that these numbers will multiply in the coming years. Ac-cording to Bernd Hugo, “The changes have cre-ated more capacity, and we're looking ahead to the anticipated growth. Besides, we want to weld other products in small batches using the robot welding equipment, and this weld-ing robot means that we hold a competitive position, allowing us to explore new markets.”