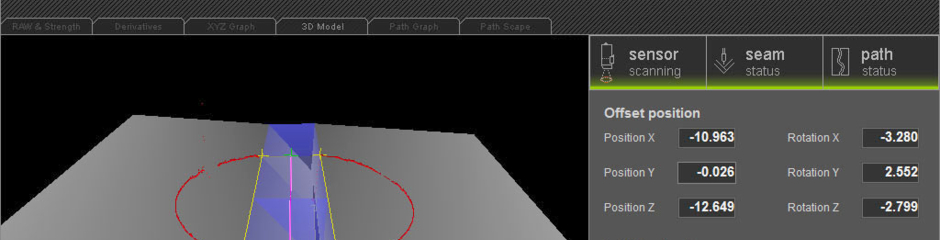
Denmark's ACO Engineering is at the cutting edge in the design and construction of thermoplates, which the company uses in equipment such as heat exchangers for the process industry.
80 of the over 100 employees work continuously on welding the thin-plate stainless steel thermoplates. The company has been working on robotising the proc-ess for some time, but keeps coming up against problems concerning the welding robot's inability to track the welding seam. The use of the Arc-Eye laser sensor means that ACO Engineering is now able to weld the first thermoplates with a welding robot.
The thermoplates are made of thin- plate2 mm stainless steel plates that are welded on the top side. The plates are easily deformed during the welding process due to their thickness and the large amount of heat applied. This presents a huge obstacle to automating the process. The plate deformation cannot be reduced, which makes it impossible to correct the deviations in the welding program. Only a laser sensor on the robot is able to continue to follow the welding seam realtime. Valk Welding has developed its Arc-Eye system for that purpose to the extent that the laser sensor communi-cates directly with the robot control. The Arc-Eye laser sensor is mounted in front of the welding torch and carries out circular scans to make a complete 3D image of the welding seam without being affected by reflections from the stainless steel.
The Arc-Eye thus determines the track to be followed by the welding robot so that a exact and reliable welding seam is obtained.
Welding robot serves two 6.5 m clamping benches
The heat exchangers, which are used in the food, dairy and chemical industry as well as in the process industry, have to meet the strict requirement set in those sectors. The thermoplates are therefore TIG welded in order to eliminate leak-age . For that purpose the Valk Welding welding robot system is equipped with a TIG robot torch and serves two 6.5 m working stations which are served in turn by the robot on a 14 m track. ACO Engineering is able to weld both the largest thermoplates of 6 x 2 m as well as the smaller versions on the robot.
Welding robot four times quicker
A heat exchanger is made of 50 up to 200 plates. A manual welder easily spends 20 hours on welding a large thermoplate all around. The welding robot does that in a quarter of the time with a higher degree of accuracy and above all, a constant quality. ACO Engineering therefore does not only achieves cost savings but also greatly improves its quality. By using the weld-ing robot system the company is now able to increase its productivity and use a number of manual welders for less monotonous work.