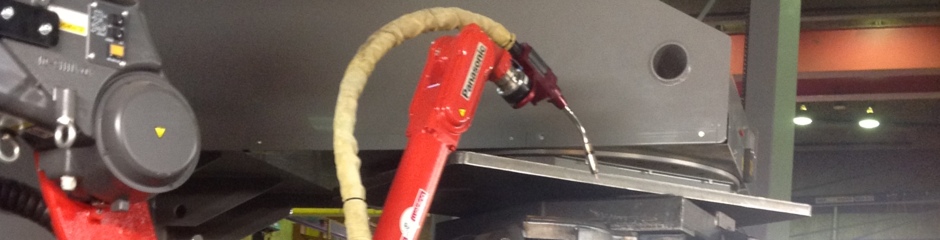
Thick plate technology simplifies Multi-Pass Welding
In close consultation with Panasonic Welding Systems, Valk Welding has developed specific technology for the multiple layer welding of thick, heavy plate sections using Panasonic welding robots. This Thick Plate technology is based on a combination of welding seam detection and specific Thick Plate welding technology software. Thick Plate software used in combination with Valk Welding's laser sensor welding seam detection makes it possible to closely monitor the welding parameters (WPS) during production. Thick Plate technology plays an important role in welding robot applications for the construction of digging machinery, steel structures and heavy transport. With the Thick Plate technology Valk Welding has since installed several welding robot systems for thick, heavy plate sections at companies including VOP and Huisman in the Czech Republic and China, Caterpillar Nederland, Victor Buyck in Belgium and the Danish Sj?rring Maskinfabrik.
When joining thick and heavy plate sections situations often arise where there are large tolerance differences and where big cracks form owing to the uneven, imprecise connections that have to be filled in several layers. Because of the big differences in the welding seam preparation, manual programming calls for a large number of teaching points, which makes the process very time-consuming.
The use of Thick Plate software makes it possible to use fast search macros and gas head and laser sensor technology to quickly and easily establish the product tolerances. By detecting only the first layer, the software automatically builds up all of the layers. The use of Thick Plate software thus makes the entire programming process a good deal easier and may also make it possible to directly correct tolerance differences in the welding programmes during production. Welding parameters can be easily registered beforehand by carrying out test welds.
Online programming: limited returns
In heavy industry most welding robot systems are programmed online, which can easily take a couple of weeks for each product. During all of that time the welding robot is out of production, which results in these relatively expensive systems having low returns. Also, online programming is less precise with regard to stick out control, which reduces the WPS reliability. Offline programming is not subject to these limitations and makes it possible to write welding programmes outside of production based on 3D CAD product data. For this purpose Valk Welding uses Panasonic's programming and simulation software DTPS, in which the Thick Plate software is added as a plug-in.
A pendulum movement and constant arc length measurement make it possible to have the stickout and the width tolerance taken up in real-time by the Thick Plate Arc-Sensor in combination with adaptive weaving.
Sj?rring Maskinfabrik deploys Thick Plate technology
Since the beginning of this year Sj?rring Maskinfabrik in Thisted has been using a fully automated welding robot system to weld components for goods such as Volvo digging machinery. The system consists of an X, Y, Z displacement of 5,000, 3,500 and 2,000 mm respectively. The working area of this robot system contains an L-shaped product manipulator with a maximum load of 5,000 kg. The robot system is equipped with a Panasonic TAWERS welding robot featuring Thick Plate software. Thick Plate software makes it very easy to use multiple level welding technology, which minimises the programming of this welding robot system. Using the welding robot TA 1900 WGH (450 Amp. at 100% arc duration) makes it possible to achieve cycle times of 6 to 8 hours without any difficulty.
Switch to offline programming
Sj?rring Maskinfabrik, which has 10 years' experience with similar welding robot systems, has succeeded in reducing the programming time by more than 60% by using the Thick Plate software in combination with the DTPS offline programming system. Also, the "touch up time" (corrections to the programs written offline) has been reduced to 0. As a result of this Sj?rring Maskinfabrik has quickly been able to write several programs of its own for this welding robot system, which - just six months after being delivered - is fully automatically welding a wide range of products, and the arc duration of the welding robot is much longer than previously owing to the offline programming.
Single piece production
Sj?rring Maskinfabrik sets strict flexibility requirements for the new system. The most important requirement was also to be able to weld single piece items with the welding robot. That is why an automatic product delivery and removal system has also been chosen in addition to complete offline programming. Product pallets for a wide range of products are placed in a fully automated warehouse in the direct vicinity of the welding robot system. That makes it possible to automatically load and unload products with an overall weight of over 5,000 kg from the working area in the robot system. The accompanying welding programme is automatically linked to the work piece being welded.