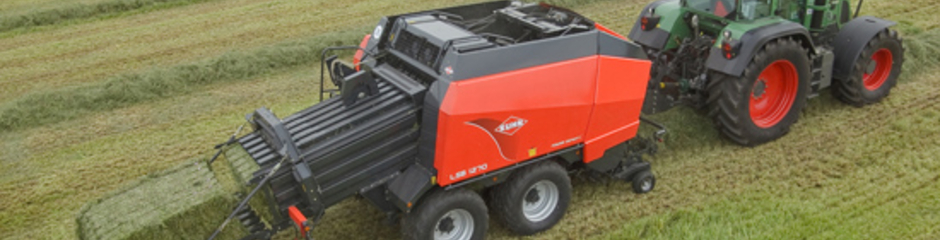
KUHN-Geldrop BV, one of the Netherlands' biggest agricultural machinery manufacturers, is one of the early adopters in the area of robot welding.
As PZ Landbouwmachines (Zweegers), later taken over by KUHN, the company has been a customer of Valk Welding's since the nineteeneighties. Johan Brandes, coach parts team, has therefore experienced the development and progress of all of the welding robot generations. KUHN now has six welding robot systems, the most recent of which is on an E-shaped structure. "We work on getting the most out of the welding robot systems in partnership with the people at KUHN and Valk Welding. We consider not just the welding robot, but also everything else involved, such as welding wire, the wire feed, operator training, aftercare and even the internal relocation."
Valk Welding delivered the two welding robot systems on an E-frame to KUHN in Geldrop in order to replace and extend the capacity. Both systems feature a Panasonic robot type TA 1900 WGH3 with the unique Weld Navigation system. Both robots are mounted on a torsion-free E-frame with 2 stations equipped with a PanaDice 1000 kg external shaft manipulator. Johan Brandes: "We weld two hundred different welding sub-assemblies on the welding robots. The good thing about the E-shaped frame is that you can clamp several small objects next to each other on it and leave the welding robot to get on with the work while you clamp new products onto the adjacent station. The very short reconfiguration time from one station to the other enables us to achieve a much higher switching duration than the other system concepts."
Robots on Eframe completely movable
The choice of a torsion-free frame was initially made in response to the relocation plans. Both frames can later be moved as a whole to the new location and put virtually straight back into use. Johan Brandes: "The welding robots of another supplier do not have that advantage, and have to be completely dismantled and reassembled at the new location, and then completely reprogrammed/ corrected. That takes a lot of time and money."
Welding wire drum no longer on trolley
"But the fact that the people at Valk Welding also give careful thought to the peripherals serves to increase the welding productivity. Take the use of the Wire Wizard wire feed system, for example. This feeds the welding wire smoothly over a distance of over 10 metres to the welding robot, and the drum can be placed at an easily accessible place outside of the system. With the welding robots of other makes that we use, the vessel moves with the system on the trolley. Placing a full drum causes a lot of positioning problems and increases the chance of damage being caused by having to shift 250 kg. The pneumatic shutdown system is another good example, also a product of welding know-how. In the event of a crash the welding robot is shut down much more quickly by the pneumatic shutdown system and we are able to put the robot back into use within a few minutes, without any complicated calibration procedures. Valk Welding carefully considers aspects such as these, which raises the OEE (Overall Equipment Effectiveness) of our welding robots to a very high level."
Big gains from offline programming
The biggest advantage of the transition to the latest generation Panasonic TA 1900 WGH3 is that the offline programs could be directly transferred from Panasonic DTPS. Johan Brandes: "Since there was virtually no difference between the two generations after the conversion, we had the robot system up and running after just 2 days. We've been working with DTPS for quite some time. We import the 3D product from CAD and set up the welding program in DTPS. If the programming is right, we can transfer it to the welding robot virtually without any corrections. During all that time the robot just gets on with its work."