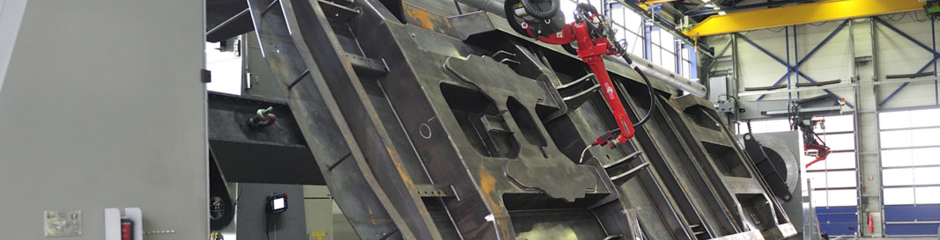
Together with eight other VDL companies for the Europe Container Terminal (ECT) in the Rotterdam seaport, VDL Containersystems has developed an Automatic Guided Vehicle (AGV) that can be used to unmanned sea container transport. The first AGVs were welded entirely manually, but VDL Containersystems recently installed a welding robot system from Valk Welding. VDL will be programming some of the welding programs for the welding robot itself using Valk Welding's offline programming system. That will not only save VDL a great deal of time with the welding work, but will also guarantee consistent quality.
ECT Rotterdam, Europe's biggest container transhipment company, has already been using AGVs for twenty years and asked the VDL Group to develop a new, replacement model at the end of 2009. A completely new generation of diesel hybrid AGVs was developed and built in just 12 months. This was done under the management of VDL Containersystems in close partnership with VDL Steelweld. The development concentrated on lowering the maintenance costs and power consumption. Based on the prototype ECT Rotterdam has placed an order for 85 AGVs that VDL is to deliver in 18 months.
Turnkey project
The new AGV has an overall length of almost 16 metres and weighs 27,000 kg. Virtually all of the welding work on the AGV is done at VDL Containersystems. The power pack and wheel suspension are then assembled at VDL Containersystems, after which VDL Steelweld in Breda deals with the system integration. The chassis alone involves 600 m of welding. Company manager Mark Verdonschot: "The VDL Group's policy is to continue to produce competitively in its own country. That is only possible with automation, so using a welding robot for this project made perfect sense. Because the AGV project is already completely underway, there was a need for the fast delivery of a properly working welding robot system. Welding robot integrator Valk Welding has ample experience of turnkey projects and has already made very good progress with offline programming. Valk Welding was able to work simultaneously on both the hardware and the programs. One of our employees spent 1 day a week in Alblasserdam during the project to write the programs for the wheel suspension and the power pack under Valk Welding's supervision while the Valk Welding programmers programmed the chassis. The turnkey Valk Welding system was delivered in March, and the chassis was welded within the agreed takt times."
600 m of welding per AGV
The product is divided into several steps to ensure that the welding robot can reach all of the welding seams. First of all components are added to a jig and attached to the chassis. These components are then welded on the robot. These steps are repeated a number of times until all of the components have been attached. Mark Verdonschot: "The welding robot makes it possible for us to weld a chassis three times faster. That not only enables us to achieve a high level of efficiency: we are also able to consistently maintain the welding quality at a high level. By using robots we expect to be able to deliver the required numbers in 18 months, without having to work in shifts. We can always change gears if necessary."
VDL Containersystems
VDL Containersystems develops, produces and sells a wide range of hydraulic container handling systems. The company specialises in hook lifts, gantry lift and cable systems, container trailers and containers for lorries, trailers and agricultural vehicles. Spreaders and automatic guided vehicles (AGVs) are made for the transhipment of ISO containers. Service and after sales are provided by a worldwide network of local partners. VDL Containersystems is a division of the VDL Group, an international industrial company comprising 81 operating companies in 18 countries and employing over 9,100 people.