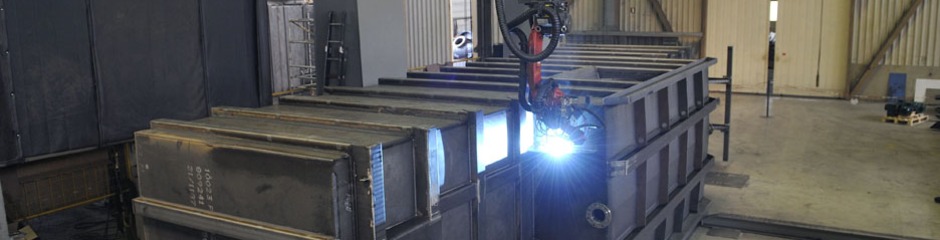
Welding robots leading factor for the rest of the production process
Last year the tank and machine engineering company GEMS in Vorden, Gelderland (NL) completed a rigorous conversion from manual to robotised welding. At first glance that was a logical step for a company that spends 80% of its hours on welding. But GEMS has adapted its entire organisation at various levels for this. "Our company has undergone a complete change in two years", explains director Jan Grasmeijer. GEMS now welds both separate components and complete tanks with welding robots, and robotised welding has been fully integrated in the production process. Valk Welding built and installed the systems, trained the company's staff and guided the tank builder through the entire process.
With its specific area of expertise GEMS is anchored in the market for high-volume products. The company is the European production partner for an American company that rents out mobile cleantanks. Stable growth in the numbers made it possible to invest in a robot system. Managing director Jan Grasmeijer: "If you try to do that with manual welders in 3 shifts it isn't possible to guarantee consistent quality. That was the time for us to make a serious start with robotisation. It isn't hard to buy a welding robot, but incorporating it in the organisation in such a way that it pays dividends as soon as possible is a different matter altogether. Valk Welding provided us with optimum support throughout the entire process."
From rigid to flexible
Technical director Rik Grasmeijer: "We'd already had a Cloos welding robot for some time, but that only knew one trick. We had to contact the supplier for each change or new programme. That isn't how we wanted to set up our automation processes. A robot should form part of the process. That is why flexibility was the most important aspect and the output of the welding robot had to be the leading factor for the rest of the production process. That sets stricter requirements for the overall logistics, for your suppliers and for the quality of the work preparation. But if, like us, you start with flexible welding robotisation at a later stage, you can tackle this from the basis straight away. The Valk Welding welding robots are now programmed offline, and we use the CAD data from engineering as the starting point." The welding programmes are written 1 to 1 on this basis for the Valk Welding robot systems.
Tank of over 70 m3
GEMS has started with welding automation for the most high-volume product: the storage tanks measuring over 11 x 2.5 m with a height of 3.7 m. Technical advisor Alex Hol of Valk Welding, who oversaw the project from start to finish: "Perhaps not the most obvious choice to start on such a large scale, but that is the product that involves the most welding hours. For that we supplied a welding robot with a 15 metre gantry, with a 3 m cross beam at right angles to it. This is fitted with a height displacement of 2.5 m under which the robot is mounted. That makes it possible for the robot to reach the entire product. The whole system was delivered on a turnkey basis, including the program for a single type of storage tank and programming training for 3 employees. Valk Welding also converted a Cloos robot system with a Panasonic welding robot to raise productivity.”
Positioning without clamping
The large storage tanks are placed on the ground and tipped with the crane to ensure that the welding robot can complete all positions in the right welding position. Alex Hol: "This kind of volume is just a bit too big and heavy to manipulate. But this is another costly aspect, so we decided to place the tank in front of the welding robot with a tolerance of ± 10 cm. This does of course have implications for selecting the position. That is why we first have the welding robot locate the right position of the welding seams with the welding wire and gas head. The deviations from the programmed positions are then automatically corrected in the welding program and the welding robot can start work. A storage tank can now be completely welded inside and out within 14 hours, whereas it took more than 40 hours to do this manually.
Already up to standard after just 3 months
Jan Grasmeijer: "Since we had already trained a number of employees with the Valk Welding system well beforehand, the engineering had switched to 3D and we had already tackled the logistics, we were able to produce the desired production numbers on the welding robot within just 3 months. The entire welding robot process is now fully integrated throughout the organisation. We are now making the storage tanks in several versions. A prototype for a new tank model is now being completely manually welded. We'll be using the welding robots for this as soon as the orders for several articles follow. In the meantime another six employees have been trained to use the welding robot and this might raise our productivity to an even higher level."